The Final Call for PCB Regulatory Compliance for your Oil-Filled Electrical Equipment
Introduction
Polychlorinated Biphenyls (PCBs) are synthetic chlorinated aromatic hydrocarbons known for their excellent electrical and thermal properties. These characteristics, along with their chemical stability, made them popular in various commercial applications in the UK, including use as an insulating fluid in capacitors and transformers from the 1950s to the early 1980s However, due to their resistance to biodegradation and their toxicity, and carcinogenicity, PCBs have raised significant environmental and health concerns. Consequently, their use has been restricted since the early 1970s and banned in electrical equipment by an international agreement in 1986. Unfortunately, common handling facilities have led to widespread contamination of mineral-insulating oil. Oil-filled electrical equipment covers, but is not limited to, transformers, bushings, switchgear, tap changers, and capacitors.
Chemical Structure of PCB
Aroclor, a PCB mixture produced from approximately 1930 to 1979, is one of the most well-known trade names for PCB mixtures. For instance, Aroclor 1254 indicates that the mixture contains about 54% chlorine by weight. The main polychlorinated biphenyl aroclors found in electrical equipment are:
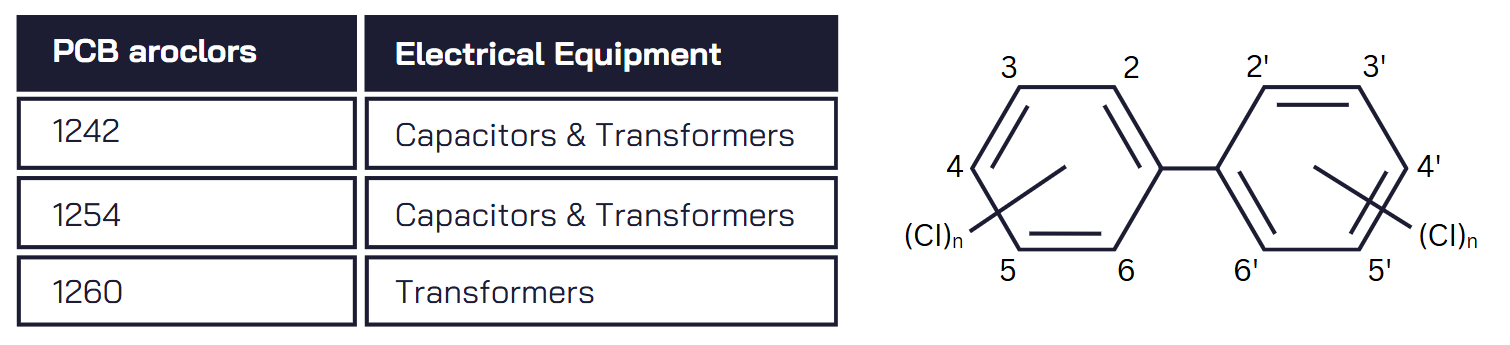
PCBs are tested by laboratories using a technique called GC-ECD using test method IEC 61619.
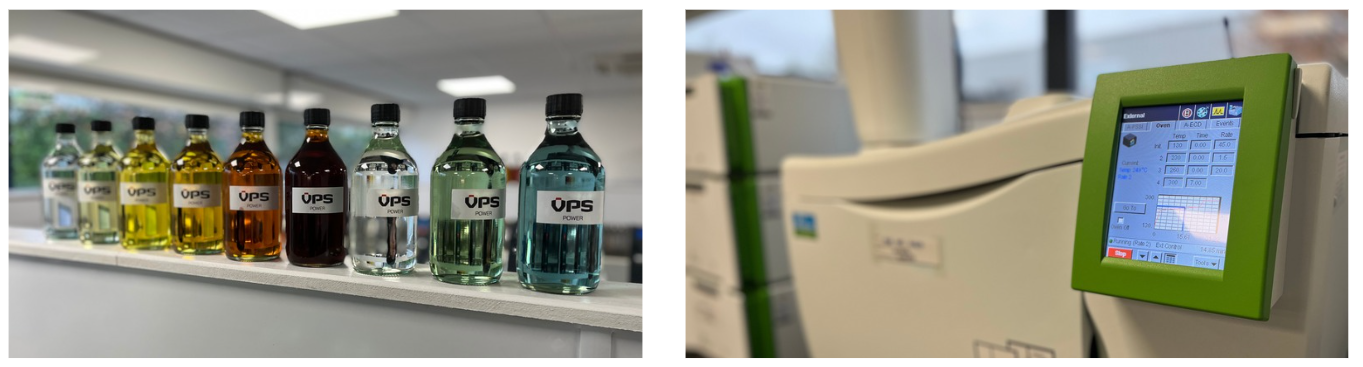
International & UK PCB Regulation
PCBs are banned internationally under the Stockholm Convention on Persistent Organic Pollutants (POP), a treaty signed in 2001 and effective since May 2004. To comply with the provisions in Part II, Annex A of the Stockholm Convention, the European Commission published the Persistent Organic Pollutants Regulation (EC 850/2004), with a recast regulation 2019/1021 in 2019. UK Government Guidance, aligned with the Stockholm Convention, states:
“Member states shall identify and remove from use equipment (e.g., transformers, capacitors, or other receptacles containing liquid stocks) containing more than 0.005% PCBs and volumes greater than 0.5dm³, as soon as possible but no later than 31st December 2025.”
You can continue to use oil filled electrical equipment until 31 December 2025 if you can reasonably assume two things about its fluid:
• It contains more than 0.005% but no more than 0.05% by weight of PCBs.
• It has a total volume of more than 0.05dm³ (0.05 litres).
After 31 December 2025, you must decontaminate and dispose of assets as soon as possible. However, you can keep an asset until the end of its useful life if you reasonably assume (and justify if needed) that its fluids either:
• Contain 0.005% by weight, or less, of PCBs.
• Contain a total volume of 0.05dm³ or less of PCBs.
After this, you must decontaminate or dispose of any PCBs as soon as possible.
When will PCB be present?
To comply with international and UK regulations, oil-filled assets manufactured before 1 January 1987 (or with an unknown year of manufacture) should be assumed to be possibly contaminated unless proven otherwise. Even if the PCB-contaminated oil has been replaced, some PCB may still be present. In the UK, PCB-contaminated mineral oil is more common than pure PCB oil-filled assets. When PCB oil was used, it was often on sites where both mineral and PCB-filled assets were used, similar to the current use of mineral and ester fluids together. During maintenance, the same oil drums and equipment were sometimes used for emptying and refilling assets, leading to accidental contamination.
Urgent Call to Action
The deadline for compliance is fast approaching. With the 31st of December 2025 deadline looming, it is crucial to act now to ensure your oil filled assets meet regulatory requirements. Failure to comply can result in significant environmental and health risks, as well as potential legal and financial consequences.
How can VPS Power help?
VPS Power tests PCBs using internationally recognized methods and the latest advanced laboratory equipment. Our certified laboratories can support your testing requirements. Contact us today at: power@vpsveritas.com